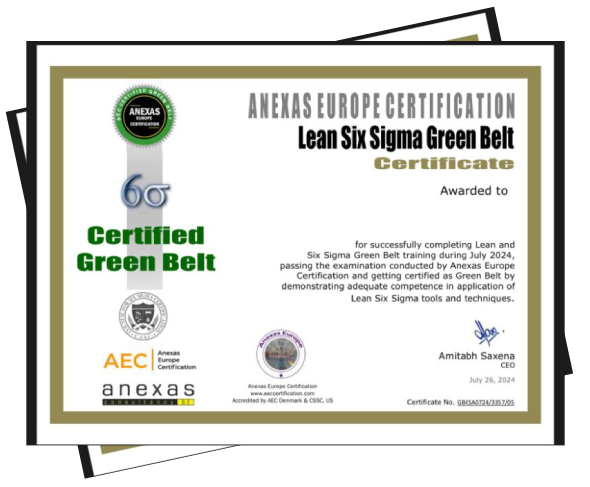
- Certificate: Green Belt in Lean Six Sigma Methodology
- ISACA: AEC
A training program that enables you to apply quality and efficiency improvement mechanisms in business processes. It combines the Loan and Six Sigma methodologies to achieve continuous improvement, reduce waste and improve customer satisfaction.
Overview of Quality and Efficiency Improvement Training Program
This training program focuses on equipping participants with the skills and methodologies needed to enhance quality and efficiency in business processes. By combining the principles of Lean and Six Sigma, the program aims to foster a culture of continuous improvement, reduce waste, and elevate customer satisfaction.
Key Components of the Training Program:
1. Lean Methodology: – Focus on Waste Reduction: Participants learn to identify and eliminate non-value-added activities in processes to streamline operations.
– Value Stream Mapping: Techniques are taught to visualize and analyze the flow of materials and information, enabling better decision-making.
2. Six Sigma Principles: – Data-Driven Decision Making: Participants gain skills in statistical analysis and process measurement to identify root causes of defects and variability.
– DMAIC Framework: Training includes the Define, Measure, Analyze, Improve, and Control phases, which guide systematic problem-solving.
3. Continuous Improvement Culture: – Empowerment of Employees: The program emphasizes the importance of involving all employees in improvement initiatives, fostering a mindset of innovation and ownership.
– Sustaining Improvements: Strategies for maintaining and building on improvements over time are covered, ensuring long-term success.
4. Customer Satisfaction Enhancement: – Understanding Customer Needs: Participants learn techniques to gather and analyze customer feedback, ensuring that improvements align with customer expectations.
– Delivering Quality Products/Services: Emphasis is placed on delivering consistent quality, which leads to higher customer satisfaction and loyalty.
